Запорная арматура — устройство и принцип действия
Запросить ценуДля управления потоками жидкостей и газов в трубопроводных системах, их линий и участков используются специальные устройства, называемые запорно-регулирующей арматурой. Данный вид трубопроводной арматуры предназначен для полного перекрытия или регулировки напора потока среды, управлением других технологический процессов, к которым относят:
- давление жидкости;
- напор;
- температуру;
- объем транспортируемого вещества.
Для каждого отдельно взятого трубопровода используется тот или иной вид арматуры. Например, устройство запорной арматуры трубопровода отличается от устройств, устанавливаемых на водных магистралях и системах перекачки агрессивных веществ.
В зависимости от места назначения и принципа действия запорной арматуры, устройства представлены в различных исполнениях.
Запорные краны
Предназначены для обслуживания участков на любых трубопроводах. Такие устройства монтируются фланцевыми или муфтовыми соединениями. При необходимости допустимо приваривать патрубки кранов к трубопроводу. Существуют две разновидности запорных кранов — пробковые и шаровые. Учитывая состояние рабочей среды, применяют различные типы кранов.
Пробковые муфтовые. Выполнены из чугуна, предназначены для эксплуатации на газовых трубопроводах. Максимальная температура рабочей среды не может превышать 50 °С. Запорная арматура монтируется в любом положении.
Пробковые сальниковые муфтовые. Также изготовлены из чугуна. Область применения – водные и нефтяные магистрали с допустимой температурой жидкости не более 100 °С. Внутренняя конструкция предусматривает наличие сальника, набитого резиновым материалом либо пенькой.
Запорные заслонки
Устройство и работа запорной арматуры трубопровода данного типа отличается от кранов тем, что запорный элемент имеет вид диска, который вращается вокруг своей оси. Ось диска расположена перпендикулярно либо под определенным углом к направлению потока рабочей среды.
Запорные заслонки нашли свое применение на трубопроводах больших диаметров при невысоких давлениях среды. Для управления заслонками могут использоваться:
- гидропривод;
- электропривод;
- ручная работа.
Материалом корпуса заслонки обычно выступает чугун, а поворотный диск выполнен из стали. Устройства монтируют на трубопровод путем врезки с применением сварки либо фланцевого соединения.
Устройство запорной арматуры газопровода должно соответствовать условиям применения и характеристиками рабочей среды, таким как:
- величина потери давления в открытом состоянии;
- особенности эксплуатации магистралей низкого давления;
- эргономичность, простота эксплуатации и ремонта;
- быстрота открытия/закрытия.
Запорные задвижки
Запорные задвижки – это трубопроводная арматура, предназначенная для периодического перекрытия потока рабочей среды. Изготавливаются из чугуна, стали (включая нержавеющую), сплавов цветных металлов. В зависимости от химической составляющей среды используются задвижки из того или иного материала.
Принцип работы данной запорной арматуры обуславливает разделение их на два вида:
- клиновые;
- параллельные.
Первые оснащены затвором в виде клина и неподвижным шпинделем.
Запорные задвижки практичны и эффективны для управления потоком среды на всех типах трубопровода – нефтяном, газовом, водопроводном.
Современные устройства оснащены электроприводом, благодаря которому можно быстро менять состояние заглушки и (или) частично блокировать поток.
Запорная арматура для агрессивных сред
Управление и регулировка потоками агрессивных сред производится с применением специальной запорной арматуры для агрессивных сред. В данном случае учитывается надежность устройств, их герметичность и время безостановочной работы.
Такими достоинствами обладают латунные запорные вентили, материал которых устойчив к большинству агрессивных сред, а трение сведено к минимуму благодаря герметичным соединениям золотника и седла.
Для магистралей с достаточно высокой температурой среды наибольшее распространение получили сильфонные запорные вентили, безупречно работающие при температуре до 350 °С. Также их применение оправдано возможностью обеспечить повышенную герметичность соединений и предупредить утечку рабочей среды в атмосферу.
Трубопроводы, которые перекачивают вещества с высокой химической активностью, в некоторых случаях оснащаются фланцевыми фарфоровыми вентилями во избежание корродирования материала. В роли антикоррозийного покрытия здесь выступает специальная глазурь, нанесенная на внешнюю часть корпуса. Для тех же случаев применяются и диафрагмовые вентили с резиновым защитным покрытием, мембрана которых выполнена из фторопласта, резины или ПВХ.
Рекомендуемые статьи
- Объём свободных нефтехранилищ в мире стремительно снижается из-за низкого спроса
Одной из основных причин значительного сокращения свободных хранилищ для «черного золота» является отсутствие желания у нефтяных магнатов ограничивать добычу, даже если это оказывает негативное влияние на ценообразование рынка нефтепродуктов. По мнению экспертов Citi, именно это обстоятельство является ключевым в проблеме сохранения доступных объемов хранилищ. Как добавляют другие эксперты энергетического рынка, нежелание…
- Метод рулонирования резервуаров
Воздухосборник (ресивер) представляет собой сосуд со сжатым газом, предназначенный для нормализации давления в трубопроводах, гашения пневматических ударов, создаваемых компрессорным оборудованием, обеспечения требуемого режима работы, сбора и удаления конденсата. Эксплуатация и обслуживание воздухосборников выполняются в соответствии с нормативами, предусмотренными для аппаратов, работающих под давлением. Общие…
- Снижение экспортной пошлины на нефть
В виду непредсказуемых скачков национальной валюты, цена на нефть стала объектом пристального внимания не только экспертов-экономистов и биржевых маклеров, но и обычного гражданина. Рубль привязан к нефти, нефть — к доллару. Влияние котировок черного золота на экономику России очевидно: растут цены, страдает социальный сектор и т.д. В сложившейся ситуации Правительство РФ вынуждено маневрировать, принимая определенные изменения…
Регулирующая арматура — Википедия
Регулирующая арматура — это вид трубопроводной арматуры, предназначенный для регулирования параметров рабочей среды. В понятие регулирования параметров входит регулирование расхода среды, поддержания давления среды в заданных пределах, смешивание различных сред в необходимых пропорциях, поддержание заданного уровня жидкости в сосудах и некоторые другие. Выполнение всех своих функций регулирующая арматура осуществляет за счёт изменения расхода среды через своё проходное сечение.
В зависимости от конкретных условий эксплуатации применяются различные виды управления регулирующей арматурой, чаще всего при этом используются внешние источники энергии и управление по команде от датчиков, фиксирующих параметры среды в трубопроводе. Используется также автоматическое управление непосредственно от рабочей среды. В современной промышленности уже редко, но все же встречается, основной способ управления регуляторами в прошлом — ручное управление (
В зависимости от параметров рабочей среды (давления, температуры, химического состава и др.) к каждому виду регулирования предъявляются различные требования, что привело к появлению множества конструктивных типов регулирующей арматуры. С точки зрения автоматизации промышленных предприятий каждый из них рассматривается как элемент системы автоматического управления технологическим процессом, протекающий с участием жидких и газообразных рабочих сред и регулирующийся под воздействием получаемой командной информации[1][2][3].
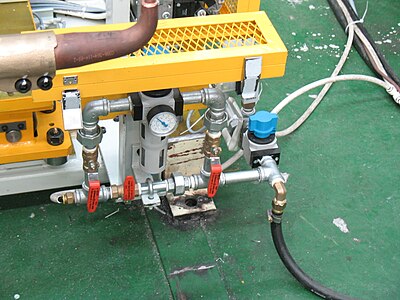
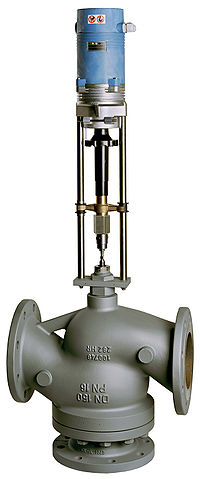
Регулирующий клапан[править | править код]
Эти устройства получили наибольшее распространение среди различных типов регулирующей арматуры. Большинство из них весьма схожи по конструкции с запорными клапанами, но есть и свои специфические виды.
По направлению потока рабочей среды регулирующие клапаны делятся на:
- проходные — такие клапаны устанавливаются на прямых участках трубопровода, в них направление потока рабочей среды не изменяется;
- угловые — меняют направление потока на 90°;
- трехходовые (смесительные) — имеют три патрубка для присоединения к трубопроводу (два входных и один выходной) для смешивания двух потоков сред с различными параметрами в один. В сантехнике такое устройство имеет название смеситель.
Основные различия регулирующих клапанов заключаются в конструкциях регулирующих органов, по этому признаку они разделяются на:
- односедельные;
- двухседельные;
- клеточные;
- мембранные;
- золотниковые[1][2].
Для управления регулирующими клапанами используются электроприводы, электромагнитные приводы и пневмоприводы. Чтобы усилия от среды и сила трения в направляющих и уплотнении не приводили к снижению точности работы клапана, используются дополнительные устройства — позиционеры[3].
Запорно-регулирующий клапан[править | править код]
С помощью этого устройства осуществляется как регулирование по заданной характеристике, так и уплотнение затвора по нормам герметичности для запорной арматуры, что обеспечивается специальной конструкцией плунжера, имеющего профильную часть для регулирования, а также уплотнительную поверхность для плотного контакта с седлом в положении «закрыто»; такая конструкция является односедельным клапаном[1][2].
Смесительные клапаны[править | править код]
Используются в тех случаях, когда необходимо в определенных пропорциях смешивать различные среды, например, холодную и горячую воду, выдерживая постоянным какой-либо параметр (например, температуру) или изменяя его по заданному закону. Отличие смесительных клапанов от регулирующих заключается в том, что управляющее воздействие, задающее положение плунжера в первых, определяет расходы одновременно двух сред, а не одной, как в регулирующих клапанах[1].
Так же, как и регулирующие клапаны, смесительные могут управляться с помощью электрического или пневматического привода (см. рис).
Регулятор с мембранным пневматическим приводом и электронным позиционером.Регуляторы давления прямого действия[править | править код]
Регуляторы прямого действия служат для поддержания постоянного давления в трубопроводе, эта необходимость может возникнуть в реальных рабочих условиях, когда в нём происходят колебания давления рабочей среды, недопустимые для нормальной работы технологической системы или установки.
В отличие от арматуры непрямого действия, в которой для непрерывного регулирования нужно отслеживать специальными датчиками состояние контролируемого параметра и при его отклонении от нормы выдавать командный сигнал приводу, регулятор прямого действия срабатывает непосредственно от среды в контролируемом участке трубопровода без использования посторонних источников энергии. Кроме таких регуляторов, арматурой прямого действия являются предохранительные клапаны, относящиеся к предохранительной арматуре, и обратные клапаны, относящиеся к защитной арматуре.
Регулирование давления может производиться после регулятора (по направлению потока среды), в этом случае регулятор называют «После себя», или перед ним, в этом случае он называется «До себя».
Принцип работы:
Предположим, что заданному номинальному давлению в трубопроводе соответствует установившийся поток среды через регулятор, при этом усилие от давления среды на чувствительном элементе компенсируется задатчиком нагружения (пружиной или грузом), то есть система находится в равновесии. При изменении давления в трубопроводе это равновесие нарушается, и затвор арматуры перемещается, преодолевая усилие от задатчика, или наоборот, поддаваясь ему, при этом изменятся степень открытия регулирующего органа, а, следовательно, и расхода среды. С изменением расхода меняется давление, и, при достижении исходного его значения, система снова приходит в равновесие, и затвор прекращает двигаться.
Наиболее часто встречаются регуляторы прямого действия, оснащенные мембранными приводами. Присоединение регуляторов к трубопроводу, как правило, фланцевое, однако встречаются регуляторы малых диаметров с резьбовым соединением (муфтовые)[1][2][3].
Регулятор уровня[править | править код]
Регуляторы уровня используются в сосудах, применяемых в энергетических, холодильных и других установках. Управляются они поплавком, по команде от которого происходит впуск дополнительного количества жидкости («регулятор питания») или выпуск избыточного количества жидкости («регулятор перелива») — статического и аститического типа[1][2].
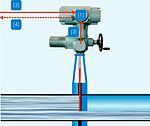
Другие типы[править | править код]
Также могут использоваться в качестве регулирующей арматуры, но значительно реже, другие типы:
- ↑ 1 2 3 4 5 6 7 Р. Ф. Усватов-Усыскин. Поговорим об арматуре. — М.: Vitex, 2005.
- ↑ 1 2 3 4 5 Д. Ф. Гуревич. Трубопроводная арматура. Справочное пособие. — Л.: Машиностроение, 1981.
- ↑ 1 2 3 4 Трубопроводная арматура с автоматическим управлением. Справочник. Под общей редакцией С. И. Косых. — Л.: Машиностроение, 1982.
Запорная арматура
Запорная арматура АРМАТЭК
Запорная арматура появилась самой первой среди всех видов трубопроводной арматуры или, правильнее сказать, тех изделий, которые позже в нее трансформировались. Долгое время она оставалась единственной и только затем, по мере ее развития, появилась предохранительная, регулирующая, обратная и другие виды трубопроводной арматуры.
На сегодняшний день запорная арматура, предназначенная для перекрытия потока рабочей среды с определенной герметичностью, является одним из самых востребованных видов трубопроводной арматуры.
Запорная арматура функционирует в режиме циклического «закрытия-открытия» рабочей полости трубопровода или в статическом режиме нормально закрытого/открытого состояния.
Устройство запорной арматуры соответствует решению ее главной задачи — обеспечить два положения рабочего органа («открыто» и «закрыто»), поэтому его промежуточное положение может не предусматриваться.
Типичная запорная арматура — это шаровые краны, задвижки, мембранные и сильфонные клапаны. Шаровые краны широко используют в различных областях техники на трубопроводах небольшого диаметра, в т. ч. при установке контрольно-измерительных приборов.
Задвижки применяют на технологических и магистральных трубопроводах диаметром от 50 до 2000 и более мм.
Установка запорной арматуры в виде мембранных клапанов эффективна, когда требуется быстрое перекрытие потока и высокая цикличность.
Сильфонные клапаны надежны в сложных условиях эксплуатации, когда недопустимы утечки во внешнюю среду, или техническое обслуживание запорной арматуры затрудненно из-за ограниченного доступа.
О комбинировании функций трубопроводной арматуры и корректном подходе к терминологии
Изготавливается несколько вариантов комбинированной арматуры, совмещающих функции запорной арматуры с функциями других видов трубопроводной арматуры.
Так, запорно-регулирующая и запорно-обратная арматура являются своего рода симбиозом запорной и, соответственно, регулирующей и обратной арматуры.
Невозвратно-запорная арматура выполняет функции обратной арматуры, будучи при этом способной осуществлять принудительное закрытие или ограничение хода запирающего элемента. Примерами ее конструктивного исполнения являются невозвратно-запорный затвор и невозвратно-запорный клапан. Запорная арматура с минимальным временем срабатывания, обусловленным требованиями технологического процесса, называется «отсечной арматурой». В «ГОСТ 24856-2014 Арматура трубопроводная. Термины и определения» использование для ее обозначения названия «быстродействующая арматура» не приветствуется. Этот же документ не рекомендует называть спускную арматуру «дренажной арматурой». (Спускная арматура — это запорная арматура, предназначенная для сброса рабочей среды из емкостей и резервуаров систем трубопроводов). Равно как и использовать в технической документации для обозначения запорного клапана слово «вентиль» из-за его неоднозначного толкования. Что, конечно же, нисколько не ограничивает применение существительного «вентиль» в повседневной речи, рекламе и СМИ для обозначения запорных клапанов, как правило, с ручным управлением.
Области применения запорной арматуры
Запорная трубопроводная арматура применяется в самых разных направлениях технологий и видах техники. В их числе имеющие огромное народнохозяйственное значение и чрезвычайно ответственные с точки зрения охраны окружающей среды атомная (и не только атомная) энергетика, химическая и нефтеперерабатывающая промышленность, трубопроводный транспорт. А также находящиеся на переднем крае научно-технического прогресса авиация, космонавтика, вакуумная техника и т. п. Монтаж запорной арматуры и ремонт запорной арматуры составляют немалую часть работ в коммунальном хозяйстве, важнейшими составляющими которого являются запорная арматура для водоснабжения, запорная арматура для отопления, газовая запорная арматура и т. д.
Входя в состав многих машин, аппаратов и оборудования, запорная трубопроводная арматура в значительной, а часто в решающей степени, как например, в случае трубопроводов, определяет их бесперебойную эксплуатацию, напрямую влияет на безопасность производственного персонала, позволяет минимизировать риски аварийных ситуаций, экономических потерь и экологического ущерба.
Больше, чем просто арматура
Невозможно переоценить роль, которую исполняет запорная арматура. Цена ее поломки может оказаться очень высокой. Сколь весомым бывает значение запорной арматуры, наглядно иллюстрируют нефтяная и газовая отрасли промышленности, в которых запорная и запорно-регулирующая арматура являются важнейшими комплектующими технологических систем, с использованием которых осуществляются добыча, транспортировка, хранение и распределение нефти и природного газа. Вышедшая из строя запорная арматура на трубопроводах ответственна за пятую часть всех аварий, приводящих к потерям сырья. В результате происшествий на нефте- и газопроводах в России ежегодно теряется несколько миллиардов м³ природного газа и примерно миллион тонн нефти и нефтепродуктов. Впрочем, перекладывать вину только на арматуру было бы неправильно, поскольку в большинстве таких аварий главную роль играет человеческий фактор, — 80%случаев потери герметичности запорной арматуры происходит из-за неудовлетворительной организации ее эксплуатации и только 20% — из-за износа или потери прочности.
Какими бы причинами не была вызвана неэффективная работа запорной арматуры, ущерб от этого огромный, а порой, без преувеличения, — катастрофический. Это не только прямые финансовые издержки в результате самопроизвольных утечек, но и порой куда большие косвенные — следствие остановки трубопровода для его ремонта. Ведь, чтобы устранить последствия отказа запорной арматуры, установленной на линейной части магистрального трубопровода, приходится останавливать транспортировку сырья, отсекать участок с неисправной запорной арматурой и стравливать его содержимое в значительных количествах. Например, из-за многокилометровых расстояний между линейными крановыми узлами на газопроводах, при отказе линейного крана в атмосферу выпускают газ из участка длиной в несколько десятков километров. Но экономический ущерб- лишь часть проблемы. Порой куда большую опасность представляют урон, наносимый окружающей среде, и угроза создания взрывоопасной обстановки.
Требования к запорной арматуре: надежность и герметичность
Базовое требование к запорной арматуре — надежность. Правильное определение показателей надежности арматуры — задача № 1 при проектировании трубопроводных систем.
Надежность для запорной, как и для любой другой трубопроводной арматуры, — это, в первую очередь, герметичность — способность элементов и соединений арматуры препятствовать газовому или жидкостному обмену между разделенными полостями. Потеря герметичности – основное проявление отказа запорной арматуры. Узлы и детали арматуры должны взаимодействовать так, чтобы образовывать соединения, делающие невозможным проникновение через них сред в любом направлении или хотя бы ограничивающие его до заданной степени герметичности.
Степень герметичности — количественная характеристика герметичности.
Жесткие требования к герметичности запорной арматуры приходится обеспечивать в чрезвычайно сложных условиях эксплуатации, под воздействием широкого комплекса нагрузок, обуславливающих процессы трения, износа, усталости и старения. Поэтому при всех видах контрольных испытаний арматуры обязательно проводятся ее испытания на герметичность по отношению к окружающей среде и испытания герметичности затвора.
Основной груз ответственности за обеспечение герметичности запорной арматуры лежит именно на затворах — совокупности подвижных и неподвижных деталей, образующих проходное сечение и соединение, препятствующее протеканию рабочей среды. На затворы приходится примерно половина всех отказов запорной арматуры, тогда как на корпусные элементы — не более 15%.
Герметичность затвора — главный функциональный признак запорной арматуры. Он характеризует его способность препятствовать обмену между разделенными полостями, обеспечивая эффективное и безотказное перекрытие потока рабочей среды независимо от ее термодинамического состояния. Затворы трубопроводной арматуры имеют тот или иной класс герметичности.
Обеспечение функциональной надежности затворов закладывается еще на стадии проектирования, поскольку, как показывает опыт, причиной немалой части отказов, связанных с нарушением герметичности, являются конструкторско-технологические дефекты. Причины отказа запорной арматуры могут быть разными, но чаще других — это износ и недостаточная плотность контакта трубосопряжений; ослабление функциональной надежности системы «трубопровод — запорная арматура».
Герметичность затвора обеспечивается максимальным сближением гладких совпадающих по геометрии уплотнительных поверхностей. Чтобы добиться нужного результата, приходится решать целый ряд сложных технических задач. Например, добиваться уменьшения шероховатости подвижных сопряжений поверхностей запорной арматуры. Для этого в технологический процесс включаются доводочные операции: полировка, притирка и проч. Но у этой стороны «медали» есть обратная сторона: получение поверхности с максимально высоким классом чистоты может оказаться экономически нецелесообразным, а, помимо этого, контакт однородных очень чистых поверхностей часто сопровождается их «прилипанием» — схватыванием за счет молекулярного взаимодействия.
Еще один путь добиться высокой герметичности — деформирование уплотнительных поверхностей в процессе работы. Благодаря упругим или пластическим деформациям, появляющимся вследствие усилий уплотнения, нагружающих конструкцию затвора, неровности на сопрягаемых поверхностях уменьшаются. Использование при изготовлении затворов неметаллических материалов, обладающих низким уровнем упругости, позволяет эти «коррекционные» нагрузки снизить и тем самым не «перегружать» арматуру требованиями к ее прочности, массе и габаритам.
В числе мер, призванных предупредить сбои в работе запорной арматуры, упоминания заслуживает не только качество запорной арматуры, ответственность за которое несут производители запорной арматуры, но ее эффективное обслуживание — своевременная замена запорной арматуры и ревизия запорной арматуры.
При разговоре о запорной арматуре невольно напрашивается аналогия с двоичной системой счисления. Подобно тому, как в той используются только две цифры — 0 и 1, функционирование запорной арматуры сводится к двум положениям запирающего органа — «закрыто» и «открыто». Сходство еще и в том, что как и сложная кибернетическая наука, опираясь на внешне такую простую двоичную систему, буквально перевернула современный мир, так и запорная аппаратура при, казалось бы, скупости возможностей на самом деле обладает огромным потенциалом, позволяющим ей занимать столь значимое место в мире трубопроводной арматуры.
Задвижка — Википедия
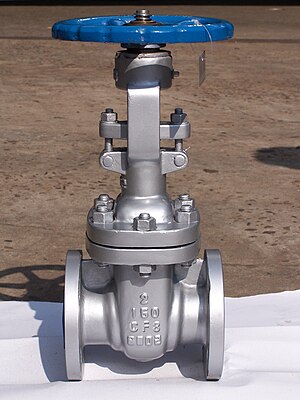
Задви́жка — трубопроводная арматура, в которой запирающий или регулирующий элемент перемещается перпендикулярно оси потока рабочей среды[1]. Задвижки — очень распространённый тип запорной арматуры. Они широко применяются практически на любых технологических и транспортных трубопроводах диаметрами от 15 до 2000 миллиметров в системах жилищно-коммунального хозяйства, газо- и водоснабжения, нефтепроводах, объектах энергетики и многих других при рабочих давлениях до 25 МПа и температурах до 565 °C[2].
Широкое распространение задвижек объясняется рядом достоинств этих устройств, среди которых:
Последнее качество делает задвижки особенно ценными для использования в магистральных трубопроводах, для которых характерно постоянное высокоскоростное движение среды.
К недостаткам задвижек можно отнести:
- большую строительную высоту (особенно для задвижек с выдвижным шпинделем, что обусловлено тем, что ход затвора для полного открытия должен составить не менее одного диаметра прохода;
- значительное время открытия и закрытия;
- изнашивание уплотнительных поверхностей в корпусе и в затворе, сложность их ремонта в процессе эксплуатации.
За редким исключением задвижки не предназначены для регулирования расхода среды, они используются преимущественно в качестве запорной арматуры — запирающий элемент в процессе эксплуатации находится в крайних положениях «открыто» или «закрыто».
Задвижки обычно изготовляются полнопроходными, то есть диаметр проходного отверстия арматуры примерно соответствует диаметру трубопровода, на который она устанавливается. Однако в некоторых случаях для уменьшения крутящих моментов, необходимых для управления арматурой, и снижения износа уплотнительных поверхностей, применяются суженные задвижки. Некоторое увеличение гидросопротивления при этом практически не влияет на работу системы, нежелательна установка таких задвижек лишь на магистральных трубопроводах больших диаметров[3].
Наиболее распространено управление задвижкой с помощью штурвала (вручную), также задвижки могут оснащаться электроприводами, гидроприводами и, в редких случаях, пневмоприводами. На задвижках большого диаметра с ручным управлением, как правило, устанавливают редуктор для уменьшения усилий открытия-закрытия.
По характеру движения шпинделя различаются задвижки с выдвижным или невыдвижным (вращаемым) шпинделем. В первом случае при открытии и закрытии задвижки шпиндель совершает поступательное или вращательно-поступательное движение, во втором — только вращательное.[4]
Основные различия задвижек — в конструкции запорного органа, по этому признаку задвижки различаются на клиновые, параллельные, шиберные и шланговые[3].
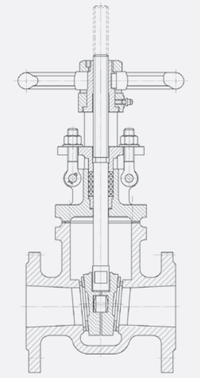
В общем виде конструкция задвижки состоит из корпуса и крышки, образующих полость, в которой находится рабочая среда под давлением и внутри которой помещен затвор (на чертеже справа он клиновой). Корпус имеет два конца для присоединения задвижки к трубопроводу (применяются присоединительные концы фланцевые, муфтовые и под приварку). Внутри корпуса расположены, как правило два седла, параллельно или под углом друг к другу (как на рисунке), к их уплотнительным поверхностям в положении «закрыто» прижимаются уплотнительные поверхности затвора. Затвор перемещается в плоскости, перпендикулярной оси прохода среды через корпус, при помощи шпинделя или штока. Шпиндель с ходовой гайкой образует резьбовую пару, которая при вращении одного из этих элементов обеспечивает перемещение затвора в нужном направлении. Такое решение (см. поясняющий чертёж) наиболее распространено и применяется при управлении вручную или электроприводом. При использовании гидро- или пневмопривода шток совершает вместе с затвором только поступательное движение. Шпиндель одним концом внутри корпуса соединён с затвором, а другим — проходит через крышку и сальник (который в основном применяется в качестве уплотнительного устройства в задвижках) для соединения с элементом управления задвижкой (в данном случае штурвалом)[3].
Заклинившую задвижку нелегко открыть даже опытным морякам.Клиновые задвижки[править | править код]
В клиновых задвижках сёдла в корпусе расположены под небольшим углом друг к другу, а затвор представляет собой устройство в виде клина — жёсткого, упругого или двухдискового, который в положении «закрыто» плотно входит в пространство между сёдлами (см. поясняющий чертёж, клин находится в нижнем положении, между сёдлами). В зависимости от условий эксплуатации выбирается тот или иной вид клина.
Жёсткий клин[править | править код]
Жёсткий клин обеспечивает надежную герметичность запорного органа, но для этого требуется повышенная точность обработки для совпадения угла клина с углом между сёдлами корпуса. Недостаток жёсткого клина — опасность заклинивания затвора и невозможность или трудность открытия задвижки в результате колебаний температур рабочей среды, износа или коррозии уплотнительных поверхностей.
Двухдисковый клин[править | править код]
Такой клин образуется двумя дисками, расположенными под углом к друг другу и жёстко скрепленными между собой. В нём диски имеют возможность самоустановки относительно сёдел корпуса, поэтому некоторые погрешности, допускаемые при изготовлении сёдел корпуса, не влияют на герметичность в положении «закрыто». Двухдисковый клиновой затвор существенно снижает возможность заклинивания, которое свойственно жёсткому клину, и, несмотря на некоторое усложнение конструкции, имеет ряд других достоинств — малый износ уплотнительных поверхностей, высокая герметичность запорного органа, меньшее усилие, необходимое для закрытия.
Клиновые двухдисковые задвижки, входящие в судовую арматуру называют также клинкетными.
Упругий клин[править | править код]
Это модификация двухдискового клина, диски которого связаны между собой упругим элементом, способным изгибаться, обеспечивая плотный контакт между уплотнительными поверхностями в положении «закрыто». В этом затворе снижены возможности самоустановки дисков по сравнению с двухдисковыми, хотя и сохраняется способность компенсировать некоторые деформации корпуса от нагрузок трубопровода и колебаний температур. Достоинства упругого клина — не требуется трудоёмкая пригонка затвора по корпусу (как для жёсткого клина) и конструкция более простая, чем у двухдискового. Таким образом, упругий клин в определённой степени сглаживает недостатки и сочетает достоинства двух других видов клиновых затворов[3].
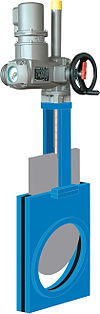
Параллельные задвижки[править | править код]
В параллельных задвижках уплотнительные поверхности двух сёдел в корпусе расположены параллельно друг другу. Затвор состоит из двух дисков, которые в положении «закрыто» при помощи специального клинового грибка прижимаются к сёдлам, перекрывая проход рабочей среде через корпус.
Шиберная задвижка[править | править код]
Является однодисковой разновидностью параллельной задвижки, в которой затвор называется шиберным односторонним. Такие задвижки применяются в тех случаях, когда допускается одностороннее направление потока рабочей среды и не требуется высокая герметичность запорного органа. Они предназначены для установки в качестве запорных устройств на трубопроводах, транспортирующих канализационные стоки, шламы, пульпы и другие, загрязнённые механическими примесями среды. Иногда затвор выполняется ножевым для разрушения частиц в рабочей среде, в этом случае задвижки называются шиберными ножевыми.
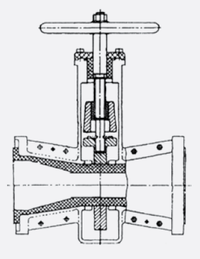
Шланговая задвижка[править | править код]
Задвижки с таким запорным органом принципиально отличаются от других конструкций[5]. Корпус не имеет сёдел, а затвор — уплотнительных поверхностей. Проход среды ведётся через эластичный шланг (патрубок), вставленный в корпус и полностью изолирующий металлические детали конструкции от рабочей среды. Для перекрытия прохода шланг полностью пережимается под воздействием шпинделя (штока), поэтому такие устройства называются шланговыми, задвижками их назвали потому, что шпиндель для управления арматурой перемещается перпендикулярно к оси прохода среды, то есть работает по принципу задвижки.
Шланговые задвижки предназначены для трубопроводов, транспортирующих вязкие, пульпообразные и другие подобные среды, а также слабоагрессивные и агрессивные жидкости. Шланги изготавливают из различных марок резин, которые обеспечивают работу задвижек при давлениях до 1,6 МПа и температурах до 110 °C[3].
Большое значение для работы и области применения задвижек имеет расположение ходового узла — резьбового соединения шпиндель-гайка. Он может быть расположен внутри задвижки в рабочей среде или вне полости корпуса.
Задвижки с выдвижным шпинделем применяют если нужно быть уверенным в надёжности арматуры.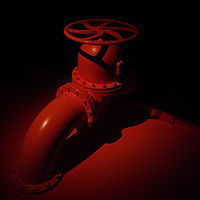
Задвижка с выдвижным шпинделем[править | править код]
В такой конструкции резьба шпинделя и ходовая гайка расположены снаружи корпуса арматуры. Шпиндель нижним концом соединён с затвором и при вращении ходовой гайки для открытия задвижки совершает вместе с затвором только поступательное перемещение, при этом верхний конец шпинделя выдвигается на величину хода затвора. Для возможности перемещения шпинделя ходовая гайка поднята над верхней частью крышки (то есть над сальником) примерно на величину хода затвора в конструкции, которую называют бугельным узлом.
Достоинствами такой конструкции являются отсутствие вредного воздействия рабочей среды на ходовой узел и свободный доступ для его технического обслуживания, а следовательно меньший износ сальникового уплотнения и более высокая надёжность резьбовой пары и сальника.
Недостатком таких задвижек является увеличение строительной высоты и массы за счёт выхода шпинделя из крышки не менее, чем на диаметр прохода и необходимость по этой причине при монтаже оставлять свободное место для выхода шпинделя.
Задвижка с невыдвижным шпинделем[править | править код]
В этом случае ходовая резьба находится внутри полости задвижки и при открывании шпиндель не выдвигается из крышки, сохраняя своё первоначальное положение по высоте. Ходовая гайка в этих задвижках соединена с клином и при вращении шпинделя для открытия прохода как бы наворачивается на него, увлекая за собой клин.
В задвижках с невыдвижным шпинделем ходовой узел погружён в рабочую среду и поэтому подвержен действию коррозии и абразивных частиц в рабочей среде, к нему закрыт доступ и отсутствует возможность технического обслуживания во время эксплуатации, что приводит к снижению надёжности работы ходового и сальникового узлов.
В связи с этим такие задвижки имеют ограниченное применение — для трубопроводов, транспортирующих минеральные масла, нефть, воду, не засорённую твёрдыми примесями и не имеющими коррозионных свойств. Поскольку в задвижках с невыдвижным шпинделем затруднены наблюдение и уход за ходовым узлом, они не рекомендуются для ответственных объектов.
Достоинством такой конструкции является меньшая строительная высота, что делает целесообразным их применение для подземных коммуникаций, колодцев, нефтяных скважин и т.д[6].
Уплотнительные поверхности задвижек изготавливаются без колец, с кольцами из латуни, фторопласта, с наплавкой из коррозионностойкой стали, из резины (в клиновых задвижках ей может покрываться клин, а в шланговых из неё изготавливается пережимной шланг).
Задвижки с корпусами из чугуна и алюминиевого сплава выполняются при помощи литья. Этим же способом изготавливаются и стальные задвижки, но некоторые из них, а также задвижки из титановых сплавов изготавливаются методом сварки заготовок, полученных штамповкой из листового проката. Такие задвижки называют штампосварными. По своим характеристикам, эксплуатационным и прочностным, они не уступают литым задвижкам, а наоборот, детали корпусов и крышек таких задвижек изготавливаются из материала более прочного и тщательно проконтролированного, качество которого выше, чем литьё. При этом технология сварки и методы контроля сварных соединений обеспечивают высокое качество корпусных деталей, позволяющее применять такие задвижки на ответственных объектах, включая атомную энергетику.[3][6]
- ↑ ГОСТ Р 52720-2007. Арматура трубопроводная. Термины и определения.
- ↑ ГОСТ 9698-86. Задвижки. Основные параметры.
- ↑ 1 2 3 4 5 6 Поговорим об арматуре. Р. Ф. Усватов-Усыскин — М.: Vitex, 2005.
- ↑ Трубопроводная арматура. Справочное пособие. Д. Ф. Гуревич — Л.: Машиностроение, 1981.
- ↑ По этой причине ранее часто именовались шланговыми клапанами или шланговыми затворами, но по современной классификации, в соответствии с принципом действия, их именуют задвижками
- ↑ 1 2 Арматура промышленная общего и специального назначения. Справочник. А. И. Гошко — М.: Мелго, 2007.